3D printing techniques speed precision materials
Introduction
3D printing, also known as additive manufacturing, has revolutionized design and manufacturing processes across industries. As a digital fabrication technology, 3D printing builds objects layer-by-layer based on digital 3D models. Recent years have seen tremendous advances in 3D printing capabilities – specifically in the key areas of speed, precision, and materials. Online 3D printing platforms have also helped democratize access to this transformative technology. This article analyzes the latest technological breakthroughs in industrial and desktop 3D printing that are enhancing efficiency, detail, and material possibilities. It also explores the role of online services in expanding applications across sectors.
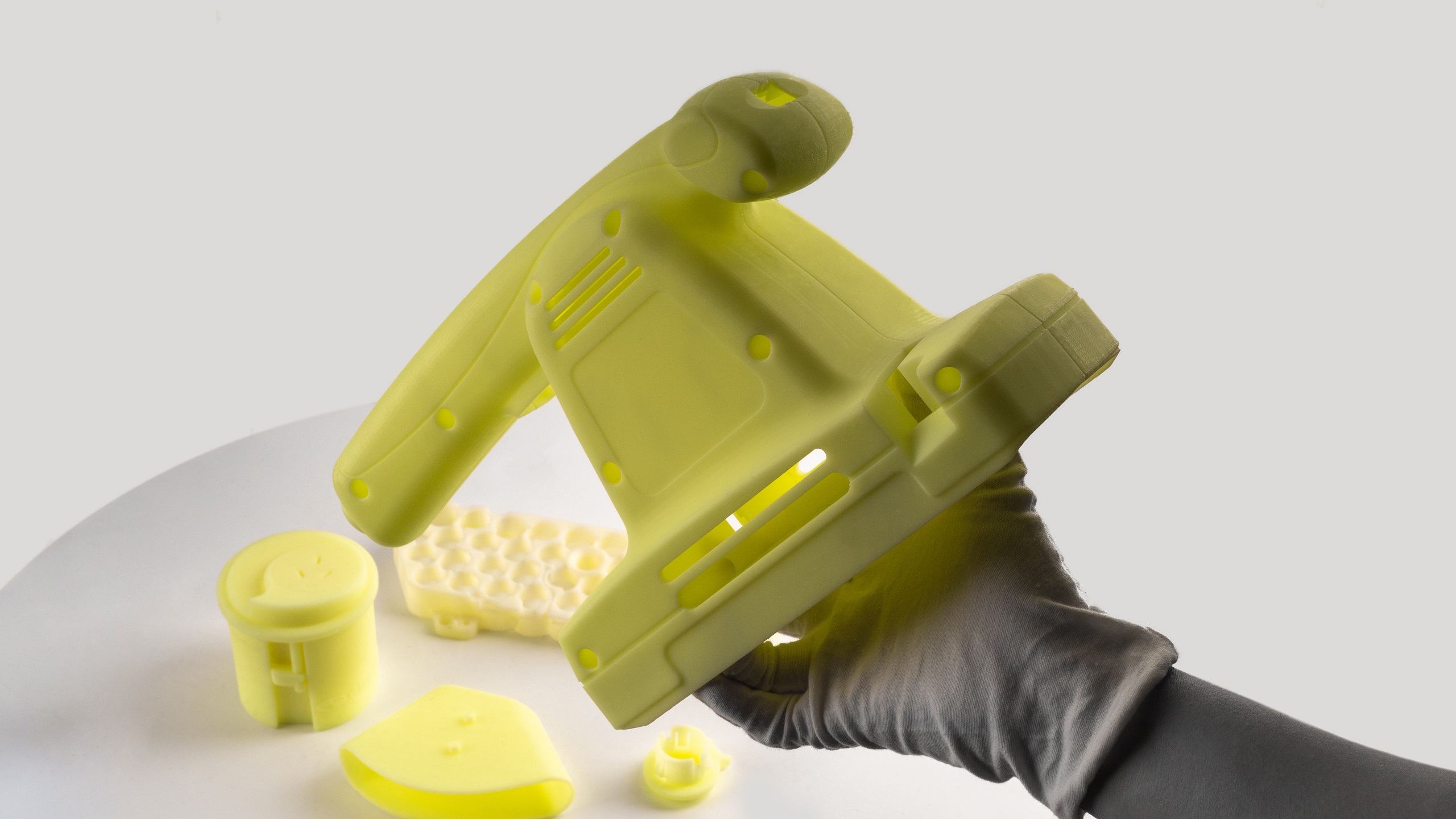
Speed: Enhancing Printing Efficiency
Traditional 3D printing techniques like fused deposition modeling (FDM) tend to be time-intensive. However, new processes have vastly improved printing speeds through innovations in hardware, software, and methods. High-speed stereolithography (SLA) and continuous liquid interface production (CLIP) use ultrafast laser scanning and photopolymerization to quickly solidify liquid resins layer-by-layer. Another technique called selective laser sintering (SLS) utilizes a laser to fuse powdered materials, enabling mass production. Through these technologies, printing time has been reduced from hours to mere minutes for small objects.
Beyond hardware, software advances like efficient path-planning algorithms, advanced slicing tools, and machine learning are optimizing workflow. By maximizing build volume use, minimizing travel paths, and prioritizing efficiency, the software is enhancing speed considerably. Automated calibration, optimized build preparation, and multi-axis movements also decrease printing and post-processing time. For instance, Carbon’s software platform automatically generates optimized lattice structures. Overall, these improvements symbolize a shift toward assembly line-style additive manufacturing.
Precision: Achieving High Detail
Dimensional accuracy and fine detail are vital in 3D printing, especially for delicate designs. Emerging techniques like digital light processing (DLP) and stereolithography (SLA) now permit layer resolutions of less than 100 microns using ultraviolet light and lasers to cure photosensitive polymers. These printers have inbuilt sensors, lenses, and mirrors to calibrate and control light intensity and direction, enabling precise solidification. Some metal printers also combine lasers or electron beams with CNC milling for ultra-precise hybrid manufacturing.
Additionally, advanced software automatically corrects anomalies and defects for consistent output quality. Controls like independent dual laser systems, real-time monitoring, and closed-loop feedback heighten reliability as well. Such resolutions can produce detailed micro-scale structures ideal for medical devices and electronics. The aerospace sector also utilizes these printers to prototype intricate engine parts with complex internal geometries. Therefore, new-age 3D printers promise unparalleled accuracy essential for high-value components.
Materials: Broadening Possibilities
3D printing now offers an extensive palette ranging from plastics to rubber, sandstone, metals, biomaterials, and composites. Specialty printers catering to particular materials have also emerged, broadening design possibilities. Notably, metal 3D printers like direct metal laser sintering (DMLS) and electron beam melting (EBM) produce end-use parts using alloys of aluminum, titanium, nickel, steel, or cobalt-chrome. Leveraging high heat, these methods generate fully dense metal components with fine microstructures unmatched by traditional techniques. Ceramic printers and cold spray processes have also made ceramics and glass viable options.
Accessibility of metal and ceramic 3D printing unlocks their applications across aerospace engines, healthcare implants, automotive, and manufacturing. Multi-material printing further enables parts with composite properties by integrating distinct materials like polymers and metals seamlessly into one object. This permits customized material properties within a single build, adding functionality. The ability to locally tune texture, strength, conductivity, and more opens an array of possibilities for product designers and manufacturers, augmenting 3D printing’s versatility.
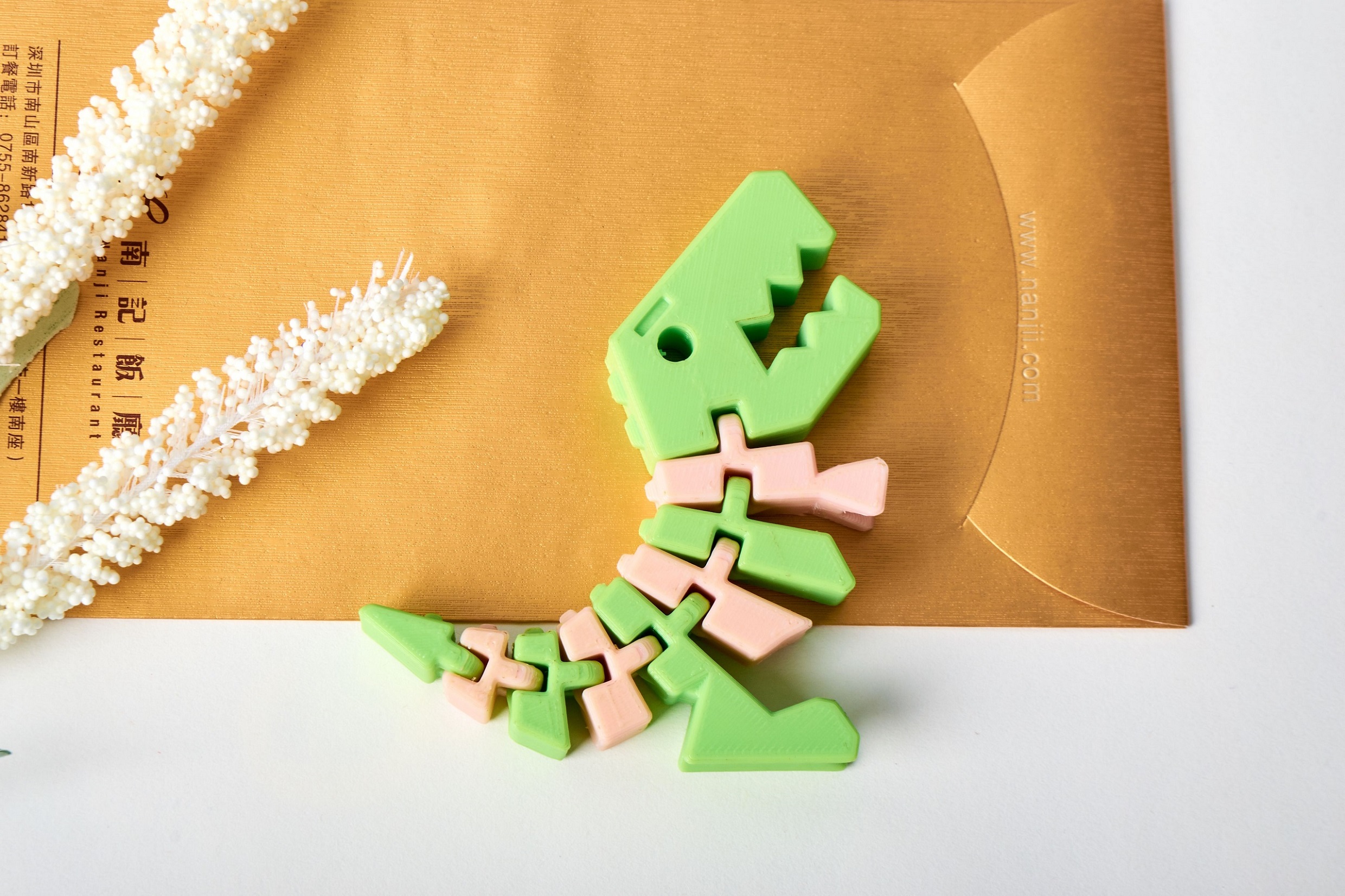
Role of Online 3D Printing Services Platforms
Online 3D printing services have played a vital role in increasing technology adoption across consumer and industrial sectors. Platforms like Qsyrapid, Xometry, Sculpteo, etc., provide intuitive applications for 3D model uploads, automated quotes, and order fulfillment through their manufacturing partners. Some also operate vast 3D printing facilities in-house using diverse technologies like selective laser sintering (SLS), fused deposition modeling (FDM), stereolithography (SLA), and direct metal laser sintering (DMLS) to produce plastic, metal, ceramic, and composite prints.
These services offer businesses and hobbyists an economical avenue to obtain customized 3D printed parts on-demand without upfront capital investment in printers or materials. Additional services provided to smooth procurement include design analysis for manufacturability feedback, part optimization for production, surface finishing methods like dyeing, coatings, or vapor smoothing, along with global shipping and logistics. By aggregating collective orders and optimizing production workflows, online bureaus drive economies of scale to keep costs affordable.
Beyond part production, online networks also enable collaborative opportunities for designers, engineers, artists and makers to engage as communities. Through forums, knowledge bases and analytics dashboards, they share best practices, troubleshooting insights, innovative applications across industries, and even partner on projects. These thriving ecosystems democratize access to leverage collective intelligence, accelerating 3D printing advancements. By lowering barriers and facilitating peer exchange, online marketplaces will be pivotal in propelling additive manufacturing mainstream across economic sectors.
Challenges and Future Directions
While additive manufacturing has shown promising growth, production consistency, and quality assurance remain persistent challenges, especially with novel materials. Currently, parts still exhibit variations stemming from build defects, mechanical properties, dimensional tolerances, and surface finishes. Standardization of processes, calibration methods, post-processing, and real-time analytics will, therefore, be critical moving ahead. More research focused on novel material interactions, modeling simulations, and reliability testing can also improve production maturity.
Additionally, sustainability considerations around energy use, waste minimization, and material toxicity warrant attention, given the technology’s environmental footprint. Exploring renewable power sources and bio-based materials are among the leading solutions. Engineers continue striving toward the holy grail of 3D printing: a fully automated and integrated manufacturing platform combining efficiency, speed, details, and material versatility within a compact production cell.
Conclusion
3D printing technology has progressed tremendously in terms of printing speeds, precision, and material versatility. Bolstered by hardware and software innovations, present-day additive manufacturing shows high throughput comparable to conventional mass production while retaining the inherent advantages of customization and geometric flexibility. With expanding printer functionalities and online services lowering adoption barriers, 3D printing is witnessing exponential growth across sectors like medical devices, manufacturing, consumer products, aerospace, architecture, and defense.
Nonetheless, consistency and sustainability remain open challenges as researchers continue expanding 3D printing capacities. Achieving the rapid, high-precision, and multi-material printing envisioned for the technology would undoubtedly revolutionize supply chains. Undeniably, additive manufacturing holds the promise of enabling localized, resilient, and agile production paradigms vital for industries of the future.
Read More
- Printing vs Injection Molding: Choosing the Right Manufacturing Process | QSYrapid•https://www.qsyrapid.com
- 3D printing – Audio plastic shell
- How to Bend Sheet Metal for 3D Printing: A Guide to Sheet Metal Fabrication | QSYrapid
- Exploring Vacuum Casting Advantages & Disadvantages | QSYrapid
- Understanding 3D Printing: Advantages, Applications, and QSYrapid Services | QSYrapid