What is SLA 3D printing? – The oldest and precise additive manufacturing method – 2024 Update
SLA stands for stereolithography, and it is sometimes abbreviated as just SL. As the name suggest, SLA 3D printing is a method of additive manufacturing where a prototype, model or functional part can be 3D printed through a process known as vat photopolymerization.
Although all these terms that describe this 3D printing technology may sound like something extraordinarily new, SLA is consider the father of additive manufacturing processes, as it is the oldest 3D printing method with a patent filed by the founder of 3D Systems, Chuck Hull, back in 1986.
How does SLA 3D printing work?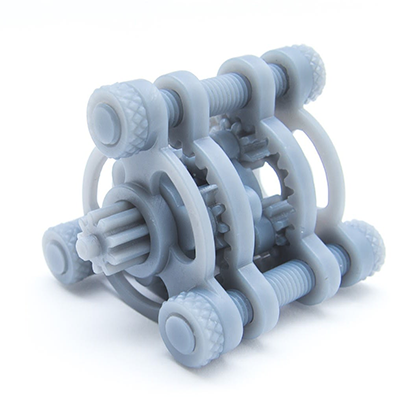
The basic working principle for the SLA 3D printing process is to produce a solid polymer by means of a photochemical process. In simple words, a liquid resin is cured by a source of light until it becomes a solid plastic. The source of light in SLA 3D printers is usually a UV laser beam which can be controlled to cure the resin layer by layer to achieve the desired results.
The materials at play here are special resins, known as photopolymers, that are designed to react and harden upon exposure to specific wavelengths of light. This reactivity is the cornerstone of the SLA process, enabling high-resolution results.
For a more comprehensive view of the process, let’s take a look at the parts and steps involved in SLA 3D printing:
1. Preparation begins with filling a reservoir with the liquid resin. Positioned in the tank is a build platform, set just one layer’s height above the liquid resin’s surface—ready for the first layer to be formed.
2. By using the information translated from the CAD model, orchestrating the laser beam along a predestined path. It does so through an array of mirrors, known as galvanometers or galvos for short, that direct the laser to targeted areas. As the laser sweeps over the resin, it hardens the liquid, layer by painstaking layer, each one mirroring a cross-section of the intended design.
3.As a newly solidified layer is completed, the printer platform shifts—either ascending or descending—facilitating the application of another layer of resin by a sweeper blade. This blade ensures an even coating, preparing the stage for the subsequent layer to form. This cycle repeats, building up the print, until the three-dimensional object is fully realized.
4.Upon the completion of printing, there comes a crucial phase of post-processing. Depending on the object’s intended use, various steps might be necessary to refine it. Initially, this involves a thorough cleaning to remove any uncured resin, traditionally using isopropyl alcohol as a solvent. In pursuit of enhanced durability or specific mechanical properties, post-curing may be employed. Additional steps could entail support structure removal, precision machining, painting for aesthetics, or assembly if the final product is composed of multiple parts.
What are the advantages of SLA 3D printing?
SLA 3D printing stands out in some aspects when compared to other 3D printing technologies. Some of the advantages of SLA 3D printing are:
1. Unmatched Precision: Of the various 3D printing techniques available, SLA is renowned for its supreme accuracy. It’s a go-to method for projects requiring micro-level exactness, making it indispensable in applications where minute detail is crucial.
2.High-Quality Creations: SLA is capable of fabricating prototypes and functional components with remarkable quality. It adeptly handles intricate designs and unique geometries, making it ideal for complex structures that are beyond the reach of more conventional manufacturing methods.
3. Ultra-Fine Layers: An extraordinary feature of SLA is the ability to achieve incredibly thin layers, with some machines claiming capabilities down to a slender 25 micrometers. This enables a superior level of detail and surface smoothness in the final print.
4. Superior Surface Finish: Objects printed through SLA exhibit a naturally smooth finish, often outshining the quality produced by other 3D printing technologies. For those seeking even greater refinement, methods to further smooth SLA prints can yield almost injection-mold level surfaces.
5. Suitability for Large Parts: SLA printing also excels in producing large-sized parts without compromising detail or quality. This makes it a compelling choice for industries such as automotive or aerospace, where large-scale prototypes are often a requirement.
6. Achieving Watertightness: Due to its layer-by-layer precision curing process, SLA printing can produce parts that are water-tight. This particular attribute is essential for applications needing containers or parts expected to operate in fluid environments.
What are the drawbacks of SLA 3D printing?
While SLA 3D printing is lauded for its high precision and ability to create complex structures, it does come with certain limitations that are important to consider. Let’s delve into the potential disadvantages that may influence your decision when opting for SLA as a manufacturing method:
- Speed Considerations: When it comes to production speed, SLA 3D printing isn’t typically the fastest horse in the race, especially when juxtaposed with other 3D printing technologies. The meticulous layer-by-layer curing process can be time-intensive, which might not be ideal for projects with tight deadlines or mass production needs.
- Support Structure Necessities: Intricate designs featuring slopes or overhanging elements often necessitate the use of support structures during the SLA printing process. These supports ensure the integrity of the part during printing but must be removed post-print, which adds time and effort to the finishing process.
- Material Fragility: SLA printed parts are fashioned from specific types of resins which, when compared to the hardiness of thermoplastics used in other printing methods, can sometimes be less sturdy. For items that will undergo rigorous functional testing or high-stress applications, this could pose a limitation.
- Resin Compatibility Issues: One aspect to be mindful of is that certain SLA printers may require proprietary resins, which can limit the interchange of materials between different brands or types of printers. This can tie a user to a specific supplier and may pose constraints on material availability or cost.
- Initial Setup Costs: When first investing in SLA technology, the upfront costs can be somewhat steep relative to other 3D printing methods, such as FDM (Fused Deposition Modeling). While SLA offers unrivaled detail and surface finish, the financial entry point may be higher, which could be a deterrent for hobbyists, small businesses, or those just dipping their toes into the world of 3D printing.
As you can see, SLA 3D printing can satisfy very specific requirements, especially those of tolerance, complex and fine details or high-quality and smooth surface finishes. However, if you are not completely sure this is the best method for you, the recommendation is to consult with an expert to avoid undesired failures and reduce costs related to repeated work in trial an error.